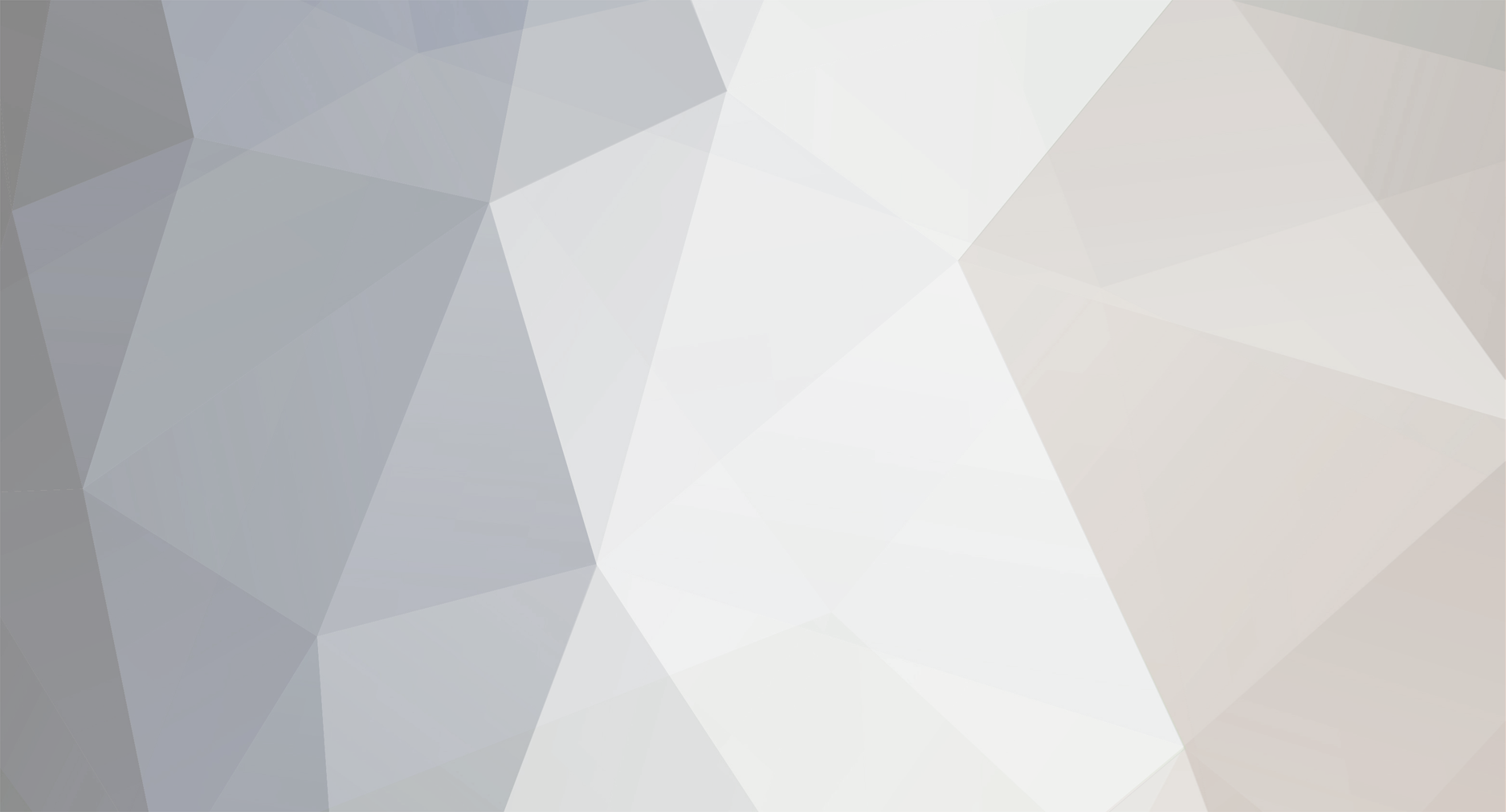
RolleyHoleMan
Members-
Posts
202 -
Joined
-
Last visited
-
Days Won
1
Content Type
Profiles
Forums
Gallery
Events
Everything posted by RolleyHoleMan
-
Making Rolley Hole marbles this year
RolleyHoleMan replied to RolleyHoleMan's topic in General Marble & Glass Chat
Here’s all the marbles in progress. The white marbles are proving to be a challenge since my grinding wheel keeps ripping pieces off them, which doesn’t happen with the black marbles. I did a lot of grinding on these and have gotten them pretty round and hopefully can start really spinning them soon. -
Making Rolley Hole marbles this year
RolleyHoleMan replied to RolleyHoleMan's topic in General Marble & Glass Chat
I’ve gotten some rock help from the rock tumbling forum. It is thought that the yellow cube and piece with a large crystal pit are calf killer agate, which is odd because it came a long ways off. Sure wish I knew where it came from. One of the locals told me to turn on the GPS photo option on the iPhone and take a photo of every rock, that way you can track where it came from. Plus write on each rock with a sharpie. Should have done that but usually I pop in somewhere before work, grab some rocks, and forget them in my car for a while. One time I wondered why my ancient station wagon was sagging a bit in the rear, and it was full of rocks. -
Making Rolley Hole marbles this year
RolleyHoleMan replied to RolleyHoleMan's topic in General Marble & Glass Chat
Got to make some rough spheres today. From what I can tell, the black material is probably actually Jasper since light only passes (poorly) through the tiniest chips and slivers of the material. I tossed a bunch of scraps into stage 1 of the rock tumbler at 60/90 grit and will have to check them next week. Jasper is the proper hardness, or so that’s what my googling says. It’s kinda odd though because I have found similar material with fossils that was blue but very soft. This stuff does seem to be very hard and well structured. So that’s a plus. When this material is wet (it’s hard to see in the photos), it has blue streaks in it. So far it has held up to spinning which sometimes causes material to explode. Also included are some photos of slabs I cut and sprayed with clear coat. This isn’t the proper way, but without a flat lapping machine or any other polishing equipment this is the best that can be done. The very colorful material is the material from roane county I have tried to make marbles from in the past, but it always breaks apart. This example seems more solid and better structured while still having cracks, so it’ll be a tough one to try. The nice thing though is with these pretty marbles, there’s no worry on size and roundness. Just get it into a sphere and round to the eye and it’s good enough, then polish it. -
Making Rolley Hole marbles this year
RolleyHoleMan replied to RolleyHoleMan's topic in General Marble & Glass Chat
Today was a general day of marble adventure. I didn’t make any marbles, but since the 10” blade came I had to give it a go. So far it cuts pretty good though it needs a lot of dressing. With every piece it needs some pieces of brick run through it to keep on going. Despite that, it cut up some darn good pieces. The best part of finding Tennessee Agate is not having any clue at all where it came from! I’ve been wracking my brain trying to remember, and all my thinking has me thinking this may have come from the Emory River in Kingston. If I knew where it came from I would sure be down there looking. When going through my scrap bucket, I grabbed a rock deemed as “no good” and cut it in half. Boy was that a surprise. Hopefully it makes a good marble though a lot of the nodule wasn’t all that great. I cut a few slabs as thin as I could get them so they can be clear coated for display. Man it’ll make a cool marble, though it only produced 2 cubes. One slab has some crystal pits which I’ve seen people make marbles from, though with the gaps I’m not sure how to go about doing it. This black material may be what they call an “agateized fossil”. It appears to be chalcedony and light does kinda pass through it, though I haven’t used the laser on it. This material came from the Tim’s Ford area outside the park at a sketchy place people were dumping poached deer. Super sketchy place with signature Tennessee trash (carcasses, beer cans, and drug paraphernalia). I got some good cubes though one piece of this black material was filled with fractures while the other didn’t seem to be, so the material may be fragile. With how my Diamond wheel is dead, there might be more ripping and tearing than grinding. Beyond that, having this blade means I should look for more rocks. I did look in the crab orchard area though to no surprise it was all sandstone. With all the traveling around the state there should hopefully be more chances to check out some rocks. -
Making Rolley Hole marbles this year
RolleyHoleMan replied to RolleyHoleMan's topic in General Marble & Glass Chat
Here’s some marble photos. Sometime I need to take some in better lighting outside, though sometimes I carry marbles in my pocket and suddenly remember to take some photos. It’s a fine marble for sure, measuring at .795. It’s one of those marbles that’ll need to be played with. When it’s time to head off to state training I’m going to organize some marbles for play by size and see if I get folks playing with a marble that suits them. One thing that’s common is the ladies say they can’t really play and show me their small hands. Granted I’ve got some big ole hands and they mention that when I’m holding marbles. Some of the best shots are women is what I always tell them. You ever been beat to a pulp by a 12 year old girl who no only doesn’t miss, but smacks the everliving daylights out of your marble? Hop on in and see what can be done. Anyways the saw blade is coming in hopefully tomorrow or Saturday, but with storms approaching there may not be any time place for cutting. Moving this saw around can be a bit wild since it weighs around 70lbs. The motor is a big bulk of that which is why I remove the motor on a similar dry-saw to help place it. -
Making Rolley Hole marbles this year
RolleyHoleMan replied to RolleyHoleMan's topic in General Marble & Glass Chat
Turns out the blade I was trying to fit onto this saw was too worn out to be much good, and it was too thin to stay properly fitted to the saw. When cutting a rock, it started to slip before freely spinning on the arbor. I ordered a Dewalt 10” blade from eBay. I did a lot of research and decided to try this blade for $42.00. A big chunk of change, so I should list some marbles. Anyways, I took a little time today to finish this marble, and it’s a fine one for sure. I opted to not polish it too much, stopping at I think 600 grit. My polishing pads need to be made into cups using PVC pipe ends and epoxy, since the marbles no longer fit in the center hole of these pads. The plan is to polish the other marbles from this nodule to see how they turn out. What’s funny is I had originally listed this nodule on eBay since it seems people have great success selling them, and I had no takers. Getting annoyed with it I cut it up and it ended up making some pretty cool marbles. seems I didn’t take a photo of the marble without the laser, but might as well post anyways after typing it all out. I’ll post a photo with other finished marbles from this nodule sometime soon hopefully. -
Making Rolley Hole marbles this year
RolleyHoleMan replied to RolleyHoleMan's topic in General Marble & Glass Chat
After an hour or so of work, I was able to remove the old blade and fit a new one. This saw was filled with a lot of junk and what seemed to be the remnants of a disintegrated blade, which is why many will harp on the importance of using proper cooling fluid with anti-rust properties. I believe mineral spirits is one of the more common fluids to use, though I have also heard of people using vehicle antifreeze, diesel fuel, kerosene, etc. it’s one of those things people like to argue about on the internet. I’m not big on spending money on these things, so I just keep with water. When I get a 10” blade I’ll clean the saw really good and go from there. I did measure and make sure this saw is indeed a 10” saw, since the internet has limited info on this old thing. When it comes time to stop with cutting, as long as everything is dried out there shouldn’t be any issues. -
Making Rolley Hole marbles this year
RolleyHoleMan replied to RolleyHoleMan's topic in General Marble & Glass Chat
Here’s some photos of the material from the Tims Ford area. Most of this material came from a sketchy little pull off in the area that was filled with poached deer carcasses. It was one nasty place. Anyways, the blade on my saw was defeated by this black piece. Whatever it is, it’s pretty cool. I kinda messed up my first cuts and made a slab too small for marbles, then the blade quit cutting due to the last bits of meat flying off in a blast of shrapnel. The photos don’t do the material justice. It’s a black chalcedony with bits of fossils in it. Super cool stuff and it seems to not be all fractured up. It does have some crystal pits but if this area has a lot of this stuff, it might be fun to bring the saw. The other piece is a nodule, though it’s microcrystalline and my last cut was too small. Not sure why so many mistakes were made today. If it makes a marble, it’ll be tiny. Plans now are to put a spare cheap blade on the saw and try to cut some material that may or may not be good. This way there’s no wasting a new blade on junk. -
Making Rolley Hole marbles this year
RolleyHoleMan replied to RolleyHoleMan's topic in General Marble & Glass Chat
Today I had a job interview for a full time position at a park im already slated to work at. I got told I didn’t get it already, however I did get to poke around the park and the staff is pretty great. So for the interview I drove nearly 300 miles total today, since Tennessee is one massively long state. The whole time I was looking for marble materials where I could. I haven’t gotten to cut anything yet, but so far it seems the area isn’t the best. Finding any material that was dense was very difficult. I got a tiny nodule that seems more like a geode, and some black chert to cut on tomorrow. Nothing too exciting, but I’m curious about the black material I found. The area had a good amount of reddish material that seems close to the fabled hard to find material Bud Garret made some famous (and expensive for the time) marbles. There’s a story he sold these red marbles in the 1930s for $35, which is the equivalent of $300 or so today. My main reason for mentioning it at all is how materials back then before the internet made a marble more valuable. Now days you can order just about anything out there. If you wanted to, you could order all sorts of agate and whatnot off the internet for a decent price and make what would have once been considered a legendary marble. One marble I’ve made in the past, that I screwed up, was a tiny pink marble that is similar to one Bud had made and sold to a local. When finding the piece in a stream, it was blood red. Of course my poor technique quickly took a decent but small piece and made it tiny, but it does have me wondering about a lot of the geology. -
Making Rolley Hole marbles this year
RolleyHoleMan replied to RolleyHoleMan's topic in General Marble & Glass Chat
Finally got around to some marbles again. It’s been a pain to get some of these decent but today I made one of the finest playing marbles I’ve seen. It was hard to decide on a finish and I may actually rough this one up a little bit since I’ve been playing with a rougher marble. The finish on it is 400 grit. This darker material came from a very small nodule one of the marble makers cut for me. He got two cubes and I got two. Since I was using a tile saw at the time I was surprised that he got that many out of it. With a tile saw I would have probably only gotten 2 cubes from it. As for the other 3 marbles, the cracked one I just went ahead and polished up. Pretty cool looking marble but it wasn’t worth more time. The other 2 are from the same nodule and I’m still working on. They are at .80 and .81, so very close depending on the size I go for. A difficulty with this material is finish. A rough marble is kinda a tan color I’d say. Polished they will look beautiful, but not wanted by most for playing. This is where white material is an advantage because you can leave it rough or polish it, but either way it’s white and doesn’t show much. Plus no one has marbles like this. Is there a reason? No idea. It seems like good material. Since I’m not s good marble player there’s no way for me to test it. At work I shoot marbles some. Playing on carpet doesn’t work all that great, same with tile and vinyl floor. You can shoot a very hard shot and your marble bounces over the target. Any spin on the marble also grips the carpet more than a dirt yard. So really smacking a marble the way you need to is pretty tricky. Also I did weigh marbles with a junky scale. A .78 marble is 10 grams and a .80 is 12. Not sure how much that means when it comes to play. One of the kids was playing with a marble that was stone, but felt like a steel ball. Wish I could have weighed it. -
Making Rolley Hole marbles this year
RolleyHoleMan replied to RolleyHoleMan's topic in General Marble & Glass Chat
Anyways, here’s the marbles I’ve been working on. I didn’t take a lot of time spinning them since I’m working on making more rough spheres while deciding if it’s time for a new Diamond wheel. I’m also still considering a saw blade as well while also working more on shaping cubes to be more easily shaped. The bottom marble is the jewel of the lot, while the top one has major faults that likely won’t be salvageable. I might just polish the top one and list it if I get around to listing marbles. I’ve been hesitant to list any more since I’ve got quite the display going with all the varieties and colors. I’ve even taken the scrap stone slabs and clear coated them (since I don’t have the tools to polish them) so people can see what material makes what marble. Edit: the large right marble is the problem marble. -
Making Rolley Hole marbles this year
RolleyHoleMan replied to RolleyHoleMan's topic in General Marble & Glass Chat
I actually have met Maggie (who wrote this) and I have her card. I was at Cummins Falls one day when a buddy of mine was doing a program on knot tying. I was screwing around trying to tie knots (I’m an Eagle Scout, I should know these things), and I made some comment about how I can’t help tie knots but I can talk about marbles. It was a joke of course. Maggie was in attendance and we started talking about Rolley Hole and a card game played at Forbes general store called “Pig”. Forbes is right up against Alvin C. York State Park, so it has that reputation Standing Stone has with Rolley Hole. Very nice lady by the way. It’s nice finding people who have the talent and abilities to report and post about this kind of stuff. It’s hard to find anyone who really wants to get into the history and lore of Rolley Hole. One major thing with festival coverage is it usually looks at the festival as a whole. These types of things mostly cover the bands playing, food, locals out enjoying it, etc, then it sidelines the actual game of Rolley Hole. So it leave the age old question of “what is Rolley Hole” mostly unanswered. This is why we want more people who know the game to walk around and really talk to people. Bobby Fulcher came up to my sister and her friends and started talking about Rolley Hole. I’ve talked about it a lot with my sister but she said “that man made marbles so precious and special”. There’s a lot more to it I suppose. One of the hardest things is getting every group and demographic interested in it. The older folks are more into the folklore and gameplay. With younger folks they aren’t all that into it unless you give some funny stories about guys getting hit in the head with a brick or meeting the Queen of England. -
Making Rolley Hole marbles this year
RolleyHoleMan replied to RolleyHoleMan's topic in General Marble & Glass Chat
As I general update, I did make another sphere today but forgot to take photos of the process. The sphere I made is the last piece of material from Powell who cut a small piece for me. I got two cubes and he got two. The cube is a dark butterscotch type color but the last marble I made from it ended up much lighter. Those guys always cut cubes pretty small too which in my hands is dangerous. One false move and a marble goes from a nice .80 to .75 or smaller. -
Making Rolley Hole marbles this year
RolleyHoleMan replied to RolleyHoleMan's topic in General Marble & Glass Chat
I’m glad to look at any source of info out there. Unfortunately I’ve spent so much time digging it sometimes feels like there isn’t anything new out there. The main thing I’ve been looking for is any documentation on marble making rigs. Everyone talks about Bud Garrets marble machine but no one knows where it is or how it works. The strong brothers also had some type of semi-automated machine that no one knows about. Seems there’s little documentation on things like that. I’ve seen some dangerous saws but that’s about it. -
Making Rolley Hole marbles this year
RolleyHoleMan replied to RolleyHoleMan's topic in General Marble & Glass Chat
Also, that reminds me. I was looking into making a wiki page for Rolley Hole. What quickly became apparent was that this would be nearly impossible because most sources are either from Bobby, or their sources are Bobby. Wikipedia will not allow this. Plus most of my info is from a combination of interviews with people (by me) and Bobby, so I'm no good for making a source acceptable from an academic standpoint. Best I can do is just keep on talking about marbles. -
Making Rolley Hole marbles this year
RolleyHoleMan replied to RolleyHoleMan's topic in General Marble & Glass Chat
I never was able to get the flint. Unfortunately I never was able to make contact with the owner. I know he in his 80s, so I also wrote him a letter since I have his address. He is located in Crossville, which is where I assume he got his material. There are many facebook listings for "geodes" for sale in that area, but you must buy it by the bucket. The videos posted by the seller are of them busting these nodules open, revealing crystals which are no good, but cool. I forget the going rate, but I want to say a 10 gallon bucket is $30. You don't know if a rock will be any good until you cut it, and I sure don't want to buy a $30 bucket of duds. Anyways when looking at geology in Crossville today, all I saw was sandstone. There's good reason all the older buildings are built with crab orchard sandstone, that stuff is everywhere. -
Making Rolley Hole marbles this year
RolleyHoleMan replied to RolleyHoleMan's topic in General Marble & Glass Chat
I've had some decent luck going through the state archives but what's always funny is that other places have much better info on Tennessee. For example I have been going through State reports from the 1930's-1970's, and a university in Illinois has all of these documents the State of Tennessee doesn't have. A lot of the old Rolley Hole literature I find online is written by "Robert J. Fulcher", known to us as "Bobby". When I see him I always have to talk some marbles. All we have in regards to Rolley Hole today is because of his Folklore project and interviewing Bud Garret. From what I was told, they were interviewing Bud about his music and he kep talking and singing about marbles. As Bobby said, "It seemed to be the right thing to look into". And it sure was. Another unfortunate thing is folklore is getting overlooked in State Parks, though people want it. They want that connection and they always light up when taken aside and given the ins and outs of Rolley Hole and any other local info. When I do job interviews my folklore stuff is pushed aside with a general "that's neat, but what else do you have". Rolley Hole is one of the last standing traditions being upheld in parks, most have lost their heritage and their history. Anyways, I didn't get to any marbles today, and likely won't tomorrow. Tomorrow might be a good day for looking for rocks or something though, probably in crossville. I keep hearing of the famous white flint over that way, but no one will say where it is. Most don't know for sure of course. A local man was offering to sell some nodules at a premium $75 per nodule, and we were willing to pay it too. -
Making Rolley Hole marbles this year
RolleyHoleMan replied to RolleyHoleMan's topic in General Marble & Glass Chat
Where did you hear about that from? I wish more people here talked about playing marbles as a kid. Most don’t really say much besides they did it. Of course the most common story is along the lines of not being allowed to play with the old men. Different people say different things about this, usually “they didn’t let me play because they knew they’d lose”. Now days most of the marble kids don’t play until it comes time to get ready for the ringer tournament in New Jersey. Or that’s what the parents tell me. But some of them kids sure can shoot. I had a kid who was 8 doing trick shots and making a fool out of me. It gets pretty funny. There’s even kids making marbles now. In my 20s I’m an old man compared to the army of kids out there making marbles. Those kids know exactly what they want in a marble and they sure know how to make it happen. -
Making Rolley Hole marbles this year
RolleyHoleMan replied to RolleyHoleMan's topic in General Marble & Glass Chat
Being around Rolley Hole I’ve seen some beat marbles, but when it comes to stone I’m starting to wonder more about the structure. Last Rolley Hole I watched a known hard-shot try to break a marble. He didn’t end up breaking it, but the force of his shots and the flash of the marbles had me really wondering. During Tennessee Square I did see a player break a shooter. He was pretty darn mad and said some choice words about it. I’m not sure what his marble was made of since I’ve heard some guys actually use ceramic marbles for that game. As far as glass marbles go, I’ve never seen impact marks, just chips and breaks. Clay marbles I bet would show more for impacts but I don’t know anyone who uses them. Lots of folks send me photos from state displays (usually archeology displays) of misshapen clay marbles, but usually they have chips. Somewhere here I have clay marbles I made in boyscouts. Maybe they got thrown away, but we made them in a fire using clay from the Tennessee river. Those things ended up with the finish and feel of house bricks. They might be something to try making again. -
Making Rolley Hole marbles this year
RolleyHoleMan replied to RolleyHoleMan's topic in General Marble & Glass Chat
Here’s something mildly interesting. I brought my unfinished marbles to work and was shooting them a good bit and with some force, causing the “crescent moons” to show up clearly on the more clear marble. The others had these marks visible as well. For the first time I really looked at these marks. Well worn marbles are covered in these marks and over time they can start to internally collapse, and eventually chip. What I think is happening is each “crescent” is a small fracture. You see the initial mark, and can follow a line deeper into the material. Since these marbles are in progress and need to be spun more, we can see how deep these marks really are. The clear marble I’m not sure how much smaller I’ll make it. It’s in the sweet spot that really works well for me. -
Making Rolley Hole marbles this year
RolleyHoleMan replied to RolleyHoleMan's topic in General Marble & Glass Chat
Last photo I forgot about. Those marbles went through the marble mill and they polished up since they weren’t bouncing. They also got oddly dark when doing this. Resurfacing them made them lighten up again. -
Making Rolley Hole marbles this year
RolleyHoleMan replied to RolleyHoleMan's topic in General Marble & Glass Chat
Here’s some of todays marble adventure. I didn’t get started until a bit later in the day, but I did keep it up for a few hours. I’m already noticing wear on my new bench grinder bushings so that’s no fun, but bushings are cheap and easy to replace. This here is a marble mill rig I set up for some quick fun. Overall it doesn’t bounce or wear smooth marbles all that well even though the grinding wheel is 60 grit, but what it does do is spin rough orbs well and gets them ready for spinning in my more valuable cups that often chip away quickly when spinning a rough marble. One of the divots I made in this wheel wore through and the marble was bouncing on the metal underneath and that happened quickly with very little pressure, so this type of setup needs to be watched. My drill press was going at around 2000 RPM and the rubber wheel is a decal eraser wheel used on cars, which is what I usually use if for. Here is a rough sphere I cut out and am now spinning. When wet it really shows some great color and it certainly a sought after material. Most cubes I have of this are very sandy so it’s hit or miss when it comes to these. Cutting the cubes down with a trim saw saved a ton of time over just leaving them as cubes. Note the left bottom marble. It is from the same nodule as the one above, but filled with sand. I have little hope for it, but if finished it’ll at least be pretty. Lately I’ve been making marbles from problematic material much larger. No point in wasting time making them small when they can’t be used. Here’s all the marbles I’m working on. The clear marble on the top right is the one that has a bad spot I’ve been wearing down. The spot is mostly gone, but the very center of it runs deep. By .78 it better be gone. The marble on the far left is finished. I had a lot of issues getting it completely round for some reason, and it’s not as tight of a tolerance I would like but it is in spec for the average marble. Some of us just get more hardcore with roundness. It’s off by maybe .002 or so, but I can’t remember for sure. You can’t tell by feel or looking at it. Either way it’s a fine shooter and once done I shot it a bit and it’s one I’m accurate with, so it’s in that sweet spot for me. What im thinking of doing is having 4 of these more clear marbles for teaching. I was originally thinking of having 4 different color ones but was also considering marking each clear marble with a colored marker to help people keep track. The place I plan to teach marbles is pavement and this clear material seems more forgiving with potential damage. -
Making Rolley Hole marbles this year
RolleyHoleMan replied to RolleyHoleMan's topic in General Marble & Glass Chat
The worry I often have with these cracks is even if I can get them out, the marble will end up small. Some marbles I cracked at .82 or so I was only able to get the cracks out around the .75 area or smaller. So I may just leave it for now. -
Making Rolley Hole marbles this year
RolleyHoleMan replied to RolleyHoleMan's topic in General Marble & Glass Chat
Spent most of the daylight I had today cutting corners off cubes and better shaping them up to reduce wear and tear on the diamond wheel. I’ve not really got the hang of it yet, but the pieces I cut do look like a cube that’s been ground on for a good while, so it’s better than nothing. I finished one marble today, and it sure is a pretty one which the camera and my indoor photography doesn’t really capture. I started out making it a shooter and have it as round as I can get it, which is tight. When spinning it in the final polish I made a critical mistake of getting it too hot. When I rinsed it off, it seems the cooling may have caused these small spider cracks in the material. Maybe they were there and weren’t visible until the surface became highly polished. Sometimes you can spin it more and get rid of these but I’ll move onto the other marbles later. The other marbles should be fine shooters, and the material is excellent. The material from this nodule is so good that by accident I confused one of the marbles with 3 marbles given to me by Mr. Carr, a local marble maker. It took a long time to pick out which one was mine, and I was only able to do so by examining all the marbles and finding the one (mine) which did not have any “crescent moon” impact marbles from gameplay. When I made marbles at Standing Stone, I usually got to play with them or have the locals smack the fire out of them, so even the fine butterscotch marbles have impact marks from when I played Georgia Rolley Hole at the tournament. Those local boys really had a time beating me to a pulp. During British marbles they were more forgiving in the sense I wasn’t much of a threat, so others were targeted. The red material pictured came from a piece of material from Roane County, and the piece it came from kept breaking apart due to how it was layered. It might end up a pretty marble if it doesn’t explode. Locals call this stuff “paint rock” but it doesn’t seem to be the paint rock agate found in the state. At my last job interview they had a nice case of geological specimens from the State and their piece of paint rock agate was reddish and rather clear. It was tumbled and didn’t appear like the best specimen since it didn’t have the wild colorations. Of course standing in front of the display case I thought “dang, that would have been a great marble”. -
Making Rolley Hole marbles this year
RolleyHoleMan replied to RolleyHoleMan's topic in General Marble & Glass Chat
Here’s what i got to earlier. Tomorrow I hope to finish these marbles up. The more colored marbles are going to be cool, but when I started on another cube of this material it was filled with hidden sand. I’ve never had a marble/cube that bad. I’d say it could still make a cool marble. Some point soon I might start listing some more marbles. I think at the moment I only have a couple white ones listed. If I can get a couple sold off I should be able to buy a new saw blade I’ve been looking at, then work on getting more material. With potential job interviews coming up, I have more chances to go to more places to look for material. In my last interview I was asked about how much time I put into Rolley Hole, and my answer was “well, right after this interview I’m meeting someone at a gas station to buy a rock saw”. Needless to say, I didn’t get that job.